As with a lot of my posts lately this covers the last couple of days.
After an overnight cure on the sheer web in the right wing aileron trough, I trimmed the glass along the edges and did a bit of sanding to knock down any roughness. I’ll fine tune the edges before I cut out the 0.2″ notches along the top edge for the aileron hinges.

After a text back and forth with Marco I realized I had probably not made myself overly clear regarding the carbon fiber reinforcement plies. I laid up the original 1-ply BID strip for the hinge reinforcement –as per plans– before I added the carbon fiber.
However, to ensure no negative galvanic-type reaction between the aluminum hinges and the carbon fiber, I will be adding at least 1 more somewhat sacrificial ply of BID on the surface of the carbon fiber. Moreover, I peel plied the carbon fiber since I plan on installing the Melvill-style stainless steel CS hex drive screws to secure the aileron hinges to the wing. These screws have 82º heads vs the aircraft grade 100º heads, so they go a tad bit deeper into the material. Once I assess how much thickness I should add to allow for the Melvill style screws, I’ll add anywhere from what I presume will be 1-3 plies of BID onto the face of the carbon fiber… thus, the peel ply.

One more shot of the trimmed and cleaned up aileron trough sheer web layup on the right wing.

I then took a short bit of time to carefully drill out the aft nose/avionics cover forward CAMLOC securing tabs.

I then got busy on the front seat right strake pilot air vent. I made an outline (black line) of my G10 phenolic aft wall of what will be the vent housing at the very front of the right strake. Here I’m using 0.040″ thick 2024 aluminum to make a removable mounting plate for the eyeball vent.
I then drilled the mounting hole for the eyeball vent in the aluminum to match the same mounting hole in the G10 phenolic plate. Lastly, I marked an inset cut line (green) about 3/16″ inboard of the G10 phenolic plate perimeter.

After drilling the 3 mounting holes, which here serve more like alignment holes, I then cut out the aluminum eyeball vent mounting plate along the inset green line.

I then mounted it all together to check fit.

And drilled out the holes for the 3 x 8-32 mounting screws.
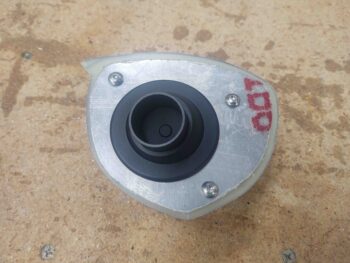
I then riveted in #8 nutplates for the 3 mounting screws. Note that at this point I have widened the diameter of the hole in the phenolic plate so that the eyeball vent housing clears the phenolic plate when mounted.

Here we have a front shot of the 3 x #8 mounting screw nutplates.

Again, the light green phenolic plate with the nutplates will become part of the aircraft structure as the aft wall of the right strake vent housing. The eyeball vent itself will be attached to the removable 0.040″ thick aluminum plate that is mounted via 3 x 8-32 screws to the vent housing.

Here’s the assemblies mounted together, from the back side.

And mounted together and test fitted in the strake.

More of a side view . . .

Here we have the strake as it looked pre-vent hole . . .

And after I used a 5/8″ hole saw to drill out the vent opening. I’ll of course do a bunch more shaping and contouring to make it look nicer and soften/round all the edges.

It was hard to grab this pic, but essentially this strake hole is very close to dead on in line with the aft intake area of the eyeball vent.
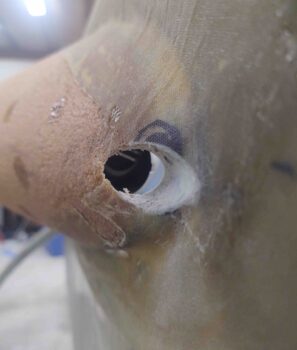
One last shot for now of the eyeball vent assembly set in place with the initial strake vent hole drilled.

My last build task for the day was spending well over 2 hours very slowly (not by choice) and carefully removing all the embedded peel ply from the top edge of the aileron trough on the left wing. This is painstaking work and is a reminder of the hours spent on removing the peel ply from the wing trailing edges!
The worst part of this, after getting the top edge done, is now I have to do the same thing on the bottom edge. Truly: Ugh!

Tomorrow my goal is to get the right wing aileron trough prepped, cleaned up and glassed.